Pre-treatment of Aluminium
Pretreatment Standards for warranty grade application
The pre-treatment process must be capable of meeting the performance outputs as described in AS3715 and AAMA-2604
Compliance to appropriate process parameters is essential in ensuring compliance to etch, conversion coating weights (time/concentration) and conductivity of the final rinse.
Etch
The etch process is a very important stage of pre-treatment and close consultation with your pre-treatment supplier is strongly recommended to ensure optimum adhesion & corrosion resistance is obtained. As an approximate guide:
- An etch rate of >1gm/m2 , is recommended for E-prime projects greater than 100 metres from the coastline, but etch rate advice from pre-treatment suppliers should be taken into consideration.
- An etch rate of >2gm/m2 is recommended for all E-prime projects between 10 and 100 metres from the coastline, but etch rate advice from pre-treatment suppliers should be taken into consideration.
Conversion Coatings
This is the next pre-treatment process for aluminium to ensure that it is suitably prepared for coating. It is recommended that Chrome conversion weights shall be a minimum of 431mg/m2, but advice from pre-treatment suppliers should be taken into consideration.
- For Chrome pre-treatment a Supplier ‘Certificate of Analysis’ should be provided by the customer and attached to Self-Assessment Declaration.
- Non Chrome conversion coatings should be applied and maintained in accordance with the manufacturer’s instructions.
- When changing from chrome to non-chrome your accreditation will require reapplication immediately. Warranty applications through this period will need to be monitored, tested and approved individually.
Final Rinse
Final rinse is to ensure optimum surface preparation prior to coating.
- Final rinse water run-off from the extrusion shall have conductivity of less than 80 micro Siemens/cm.
- The maximum time between pre-treatment and the application of the powder coating is 24 hours.
- The entire area of the aluminium shall be properly pre-treated, appropriate spacing devices should be used.
Handling
Care should be taken with handling to ensure health and safety measures are met and that the substrate is not contaminated.
- Pre-treated sections must never be handled with bare hands. Clean and lint free cotton gloves must be worn at all times when handling pre-treated sections.
Dry Off Oven (if applicable)
If your site uses a dry off oven to assist in the pre-treatment process please ensure:
- The temperature of the dry off oven must be such that the temperature of the sections does not exceed 75˚C unless advised by pretreatment supplier specifications. Applicators must be able to demonstrate compliance with this specification.
Pre-treatment of Steel
Steel substrates shall be prepared as follows:
1. Wash and degrease all surfaces to be coated in accordance with AS1627.1 with a free-rinsing, alkaline detergent, in strict accordance with the manufacturer’s written instructions and all safety warnings.
2. Wash with fresh potable water and ensure that all soluble salts are removed in accordance with AS 3894.6 methods A&D.
3. Grind all sharp edges with a power tool to a minimum radius of 2mm.
4. Power tool clean welds to AS1627.2 Class 2 to remove roughness. Remove filings, preferably by vacuum or compressed air.
5. Abrasive blast clean all steel surfaces to be painted in accordance with AS1627.4 to visual standard AS1627.9 Class 2.5 (equivalent to ISO8501-1, Sa 2.5: Very Thorough Blast-Cleaning). Use a medium that will generate a surface profile of 35 to 65 microns (as tested to AS3894.5 Method A.) In situations where it is not possible to prepare your item on all surfaces as described above, for long term protection against corrosion it is strongly recommended whenever possible, that an alternative substrate such as, aluminium be considered.
6. The steel is to be stored in an area which is clean and dry
7. The steel must be coated within 4 hours of blasting.
Application
Application Method
Electrostatic Spray
Cure Schedule
210 for 8 mins minimum
200 for 10 mins minimum
190 for 15 mins minimum
When applying subsequent coats partially cure for 3-5 minutes at 120-150°C metal temperature. This partial cure is referred to as a green cure. Refer to the E-Prime Data Sheet for full details.
Project Suitability – Perforated and Expanded Aluminium
Dulux recommend a Alumi Shield™ warranty system for both interior and exterior usage on perforated and expanded aluminium. The use of a Grey Primer/E-prime powder primer over suitably pretreated architectural grade aluminium is mandatory in conditions of high corrosivity below a recommended top coat. Although not mandatory in other areas, the use of Grey Primer/E-prime is also recommended for enhanced corrosion protection on perforated and expanded aluminium.
All Dulux Alumi Shield™ warranties are available when applied by a Dulux Accredited Powder Coater to a approved specification.
Use the following table to help identify the product and system choice you have for the perforated or expanded aluminium on your project. Refer to the conditions information to determine the environment that your project will be exposed to.
● Alumi Shield™ warranties are available when applied by a Dulux Accredited Powder Coater to the warranty specification on recommended project types and conditions
All Dulux powder products are NOT suitable in strongly acidic or caustic environments so pH must be between 5 and 9.
1. Fluoroset may be suitable in locations 10m from the high tide line.
2. Electro, Duratec, Protexture and Duralloy +Plus are only suitable for environments >10m from the high tide line.
3. Duralloy is only suitable for environments >100m from the high tide line.Information for Perforated and Expanded aluminium:
Alumi Shield™ warranties on perforated and expanded aluminium are available for products recommended for the indicated projects, environments and conditions above. Powder Primers may be necessary as detailed below:
a. Interior – General interior conditions (E-Prime/Grey Primer base coat not mandatory); Moderate Interior (E-Prime/Grey Primer base coat mandatory).
b. Exterior – Mild (E-Prime/Grey Primer base coat not mandatory);
Severe: (E-Prime/Grey Primer basecoat mandatory).
For more information about specifications on perforated and expanded aluminium call 0800 800 975 or visit here
Project Suitability – Steel
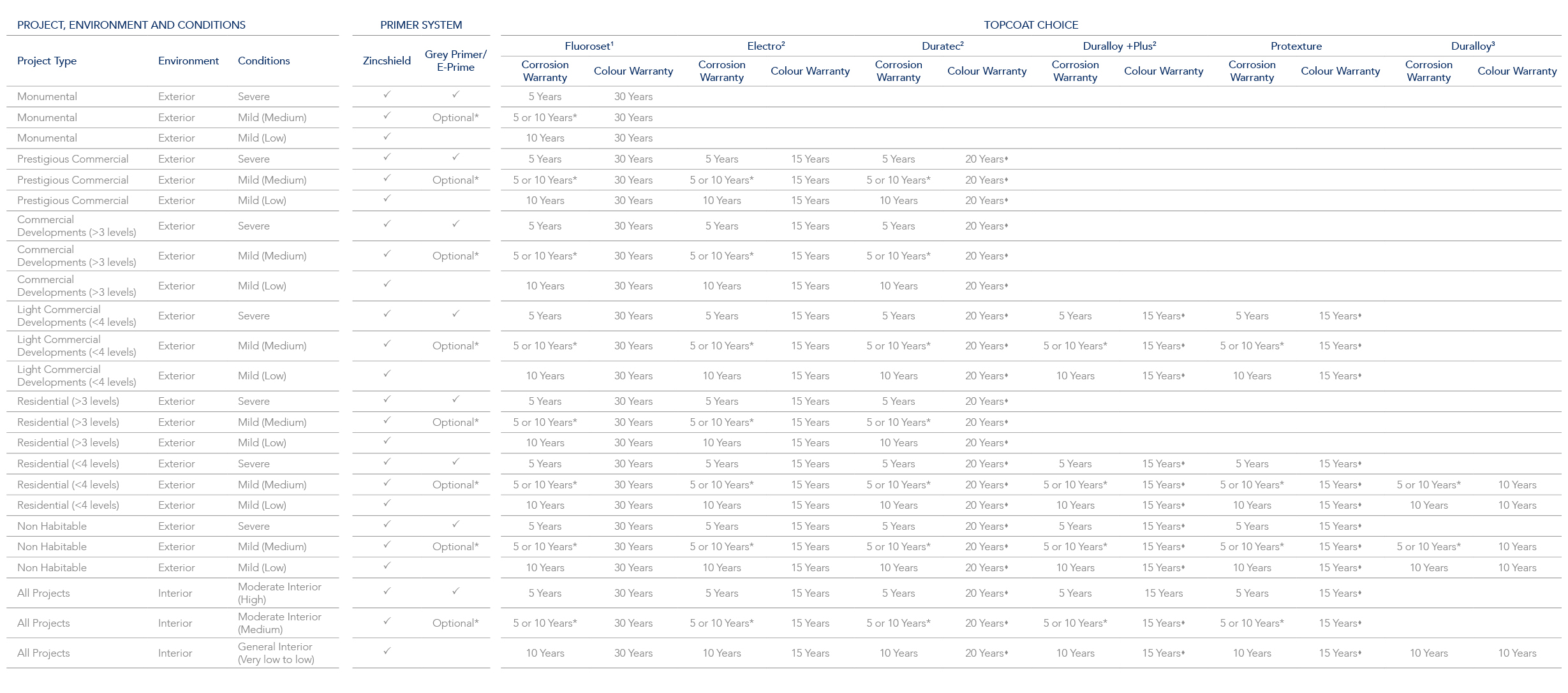
All Dulux powder products are NOT suitable in strongly acidic or caustic environments so the PH must be between 5 and 9.
1. Fluoroset may be suitable in locations <10m from the high tide line e.g. harbours (contact Dulux for advice.)
2. Electro and Duratec are only suitable for coastal environments >10m from the high tide.
3. Duralloy is only suitable for coastal environments >100m from the high tide line.
* In Mild (Medium) exterior environments and Moderate (Medium) interior environments a 10 year corrosion warranty is available with a Zincshield, Grey Primer/ E-Prime and the indicated top coat system. Without Grey Primer/E-Prime a 5 Year corrosion warranty is available.
♦ Duratec Intensity – Steel Colour Warranty 15 Years.
Please refer to Interior and exterior environments close to liquids for warranty implications where powder coatings may be in close proximity to liquids other than the sea.
Conditions – Alumi and Steel
1. Geothermal environments greater than 500m of a bore, mud pool, steam vent, or other source with a pH between 5 and 9. For pH outside this consult Dulux.
2. Geothermal hot spots within 500m of a bore, mud pool, steam vent, or other source.
3. All offshore islands including Waiheke Island, Stewart Island, Fraser Island and Pacific islands eg PNG, Fiji, Samoa, Tonga, Tahiti, Noumea
4. The corrosion rates for the first year of exposure for the different corrosivity categories of Aluminium and Carbon (Mild) Steel are determined by the following standards:
SNZTS 3404 – Standards NZ Technical Specification – Durability requirements for steel structures & components
AS 2312.1 – Guide to the protection of structural steel against atmospheric corrosion by the use of protective coatings. Part 1: Paint coatings
ISO 9223 – Corrosion of metals and alloys – Corrosivity of atmospheres – Classification, determination and estimation
5. The corrosion rates for the first year of exposure for the different corrosivity categories of Aluminium are determined by the following standard:
ISO 9223 – Corrosion of metals and alloys – Corrosivity of atmospheres – Classification, determination and estimation
Interior and Exterior environments close to liquids other than the sea
Grey Primer/E-Prime suitability for environments close to liquids other than the sea is dependent on the top coat choice.
Please refer to the guidance below for:
- Any interior application of powder coating close to liquids, eg swimming pools, fountains, bathrooms, showers, sinks etc
- Buildings that have exterior facilities close to liquids other than the sea, eg outdoor swimming pools, fountains, outdoor bathrooms
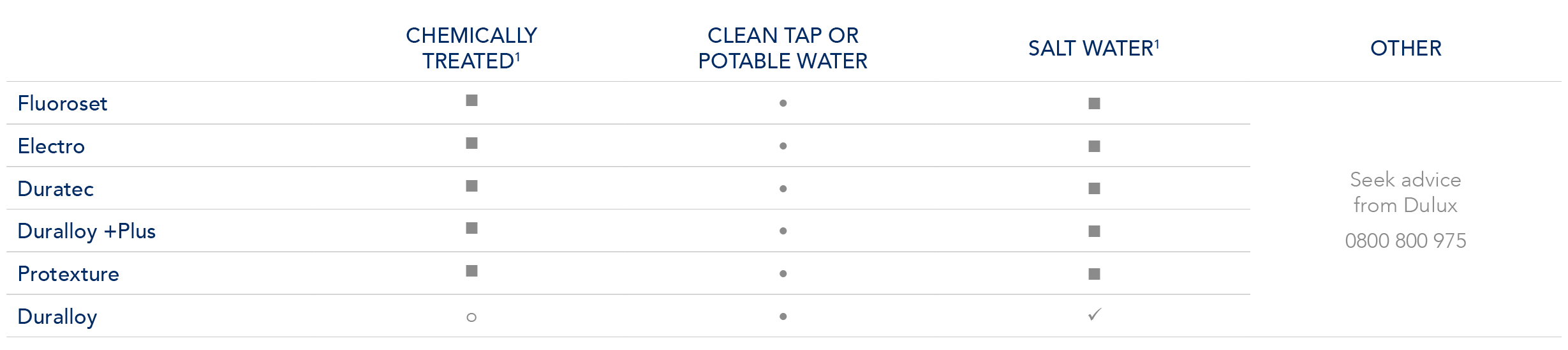
1. Aggressive liquids such as Chemically Treated liquids and Salt Water must be cleaner off immediately as per the Dulux Care and Maintenance guide.
Please note chemically treated water includes antimicrobial treatments, e.g. in pools, anti-corrosive chemicals, and soapy water in bathrooms and showers.
■ Where indicated Alumi Shield and Steel Shield warranties are available on areas >than 1m from the liquid.
✓ Where indicated Alumi Shield and Steel Shield warranties are available on areas >than 2m from the liquid (ie outside the splash zone).
○ Where indicated Alumi Shield and Steel Shield warranties are available on areas >1m from the liquid on interior applications and >2m on exterior applications
● Where indicated Alumi Shield and Steel Shield warranties are available any distance from the liquid.
Alumi Shield and Steel Shield warranties are only available when applied by a Dulux Accredited Powder Coater to the warranty specification on recommended project types and conditions.
All Dulux powder product are NOT suitable in strongly acidic or caustic environments so the PH must be between 5 and 9.
Alumi Shield and Steel Shield warranties are not available if the powder coating is immersed in any liquid.
Advice Line
Our dedicated consultants can help simplify the specification process, saving you time and money by providing the right coating advice for your project.
Call 0800 800 975.